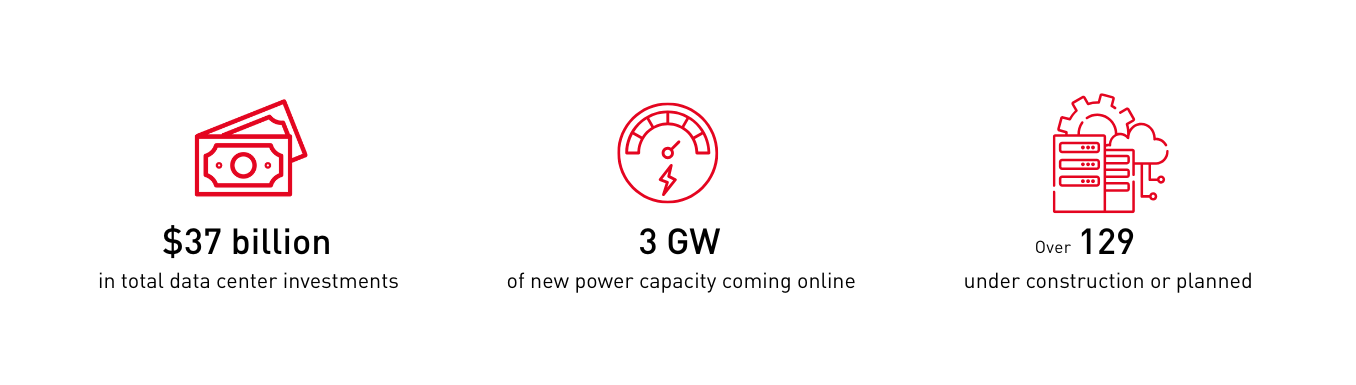
The rise of AI-powered data centers is not just increasing demand—it’s redefining the standards of precision, cleanliness, and traceability in manufacturing.
These next-gen facilities are built around ultra-dense server racks, liquid cooling systems, and high-efficiency power modules. Every component must be assembled with zero-defect tolerance, ESD protection, and full digital traceability.
While many factories in Southeast Asia still rely on manual tools and rigid processes designed for yesterday’s products, the rise of AI-driven infrastructure demands a shift to smart, connected systems built for precision, traceability, and speed.
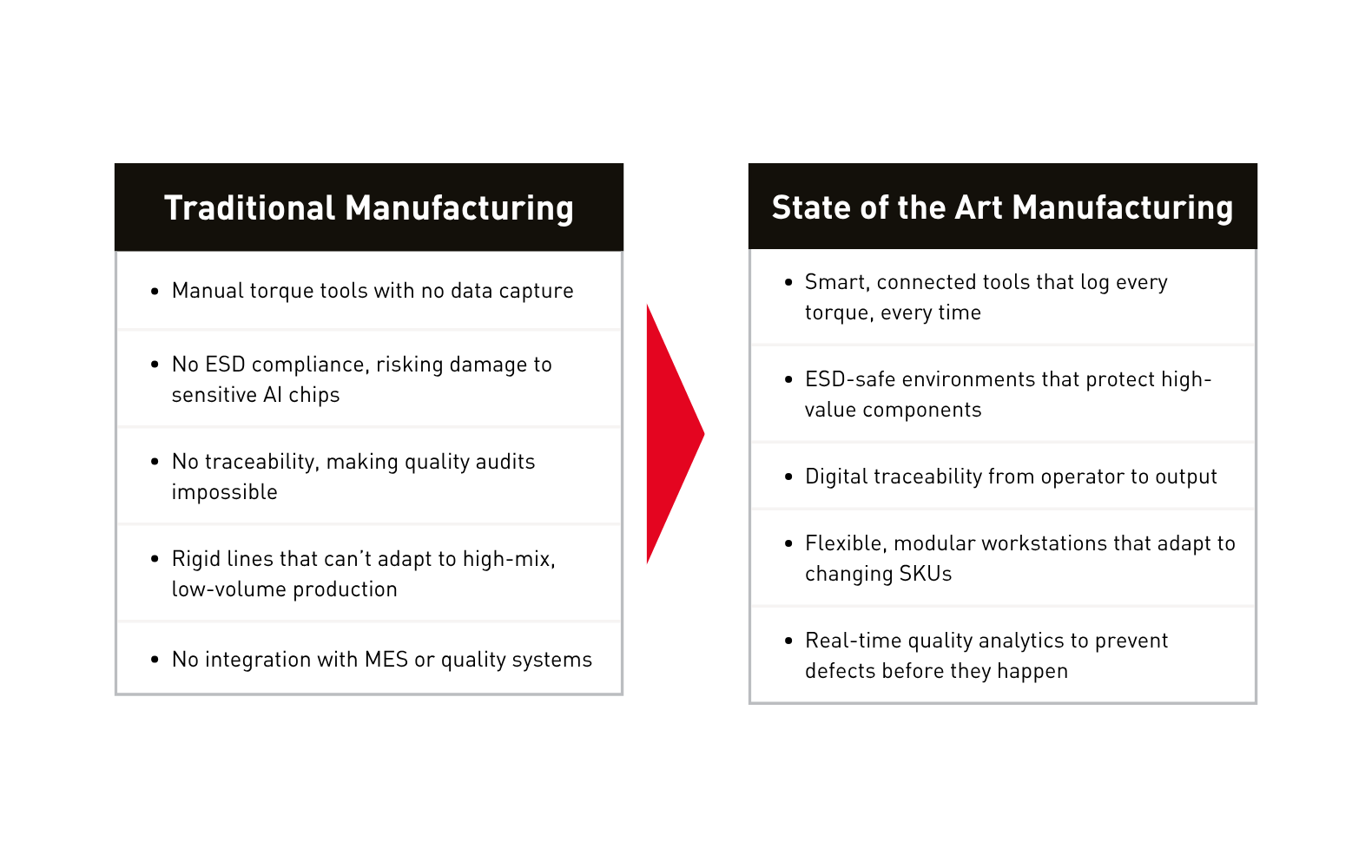
“AI data centers are built on precision. If your assembly line can’t prove it, you’re out of the game.”

#1 Rack & Server Assembly— “Every bolt matters. We make sure every one is perfect—and provable.”
Challenges: Inconsistent torque, no traceability, and high rework rates make it nearly impossible to meet the zero-defect expectations of hyperscalers.
Solution: combines smart torque tools with real-time data capture, operator guidance systems powered by PIVOTWARE to prevent errors, and full digital traceability for every fastener through DEMETER.
#2 Cooling Component Assembly—“We protect your components—and your reputation.”
Challenges: Cooling systems are ESD-sensitive and often complex, requiring high-mix, low-volume flexibility that traditional lines can’t handle.
Solution: Desoutter provide ESD-compliant tools and workstations, modular assembly cells for flexible production, and quality analytics to detect and address issues before they escalate.
#3 Power Supply Assembly—“Powering the cloud starts with precision on the line"
Challenges: Power modules must meet the highest standards of precision and reliability. One defect can mean downtime for an entire data center.
Solution: Desoutter digital torque control with programmable parameters, closed-loop quality systems, and seamless integration with MES and traceability platforms.